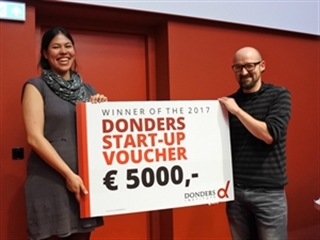
Donders Startup Voucher
2018-05-03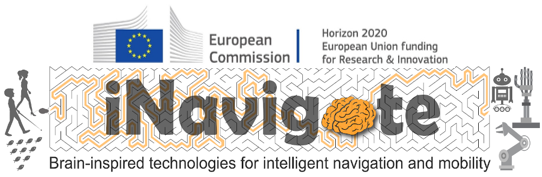
3Dneuro joins iNavigate, a Horizon 2020 consortium tackling navigation with brain-inspired methods
2020-02-11In recent years, 3D printing technology has been getting better and cheaper, bringing performance usually accessible only to large industrial companies into the consumer market. New materials are constantly developed, and nowadays it is possible to print objects with high detail in a variety of plastics, metals, and even sandstone or wood.
In neuroscience research, 3D printing is now being used – often in combination with an open source philosophy – for 3 reasons:
- To make stuff that companies won’t make for you,
- to make common technology more flexible,
- or to make crucial instrumentation less expensive.
In this article, we look at some recent examples.
CREATE
Cutting-edge research stands at the edge of knowledge, by definition, but also typically at the very edge of what can be done with existing technology: Researchers want to do experiments that are often not feasible with off-the-shelf components. DIY skills become quite valuable then. With 3D printing becoming more accessible, one can rapidly prototype on printers available for under $1000. Workshops in research institutions are now also more likely to house one or more 3D printers. So if you can imagine your solution, and the design is sound and grounded in the limitations of the 3D printing process and materials, you can print it.
A well know application of 3D-printing in electrophysiology is the Flexdrive (Voigts et al. 2013), a “novel spring-based drive mechanism that reduces implant weight and complexity” while allowing recordings and stimulation from large neuron populations in behaving rodents.0
More recent examples include microdrives for silicon probes by 3Dneuro (3Drive) or Neuronexus (dDrive), and customized implants for primate electrophysiology by the Roelfsema lab (Chen et al. 2017). In the latter, basic design templates are adjusted for each monkey based on individual modelling of their skull shape, allowing optimized implants and surgical guides in experiments where errors and imprecisions can be extremely costly. Notably, while prototyping is done with plastic, final prints are made in titanium.
MODIFY
Existing technology may come in a limited number of sizes and be restricted to certain materials. It is the case for optomechanics, i.e. the set of mechanical components used to build optical systems such as 2-photon microscopes. There a few sizes are available, and metal is the material of choice. Your custom setup will therefore inherit the limitations/features of the underlying technology platform. And deviations from typical use cases will usually require some custom parts. These design constraints might be a burden, and even make some ideas impossible to realize. It is possible to leverage the flexibility of 3D printing in order to minimize these design constraints: µCube is such an attempt applied to optomechanics (Delmans and Haselhof, 2018). The µCube system comes as a library of parts, where each file is parametric, making it possible to easily adjust the dimensions of the parts to the optical components.
And each part follows a common standard, which the authors propose as a basis for extending the library. One assumption with optomechanics is that small imperfections in machining cause small imperfections in geometry, which can in turn have a significant impact on the optical properties of your system. Therefore, a crucial step for validating the µCube concept was to build and test optical systems for alignment, which proved excellent in a fairly simple optical system (see Delmans and Haselhof, 2018 – Figure 4).
CUT-PRICE
In some cases, 3D printing is used with the sole purpose of making a measurement device more affordable. That is the case for the 3D-printed Ethoscope, a behavior quantification box for flies (Geissman et al., 2017). With DIY and 3D printing, the Ethoscope is 5 to 8 times less expensive than commercial alternatives. That means a lab could make 5 ethoscopes for the price of one commercial model, possibly give 2 away to a partner lab or a school in a developing country, and still have 3 ethoscopes. Note that in addition to removing design constraints, the µCube system mentioned earlier is also intended to reduce the cost of optical setups.
Lowering the barrier to entry for research with DIY/open source approaches is an important goal. But price comparisons between DIY/open source and commercial solutions can be tricky, and should be interpreted with caution. While companies charge for production costs and man-hours (plus costs of running a company and profit margin), DIY/open source projects are typically priced only for materials. So “device X for under $100” does not reflect its true cost. The time invested, as well as for example one-time equipment purchases, would add to the actual cost. This short analysis only scratches the surface of price and cost in academia/companies, but applied to the categories we have singled out, it allows us to conclude the following: In the context of pure competition on price, man-hours and other costs matter a great deal, and should be part of the equation. If you create or modify instead, it doesn’t matter as much.
The examples above illustrate the potential of 3D printing in neuroscience research. You can use it to create new stuff, and to modify – or cut prices of – existing stuff. This makes neuroscience research technologically more ambitious, and financially more accessible.
Thanks to its flexibility, 3D printing can have many more applications and uses. What solutions or initiatives do you know that use DIY/3D printing to make research better and/or more accessible? Let us know in the comments!
—-
Copyright: ©3Dneuro, 2018. This is an open access article distributed under the terms of the Creative Commons Attribution-NonCommercial License, which permits unrestricted use, distribution, and reproduction in any medium, provided the original author and source are credited, and the material is not used for commercial purposes.